Członkowie zespołu badawczego, którzy szerzej zaprezentowali tę koncepcję w Advanced Materials, mówią o stosowaniu nowego metamateriału między innymi w implantach, samolotach, a nawet rakietach. O jego potencjale najlepiej świadczy fakt, że pod względem wytrzymałości przewyższa numer dwa w zestawieniu aż o 50 procent.
Czytaj też: Nowa technika druku 3D nawet 10 razy szybsza od obecnych. Ale nie ma róży bez kolców
Właściwości metamateriałów nie są zależne wyłącznie od ich struktury cząsteczkowej. Ten konkretny wykazuje właściwości elektromagnetyczne niespotykane w naturze i powstał na bazie stopu tytanu. Starania w tym zakresie trwały od lat, ponieważ inżynierowie chcieli naśladować struktury spotykane w naturze, na przykład w roślinach wodnych. Niestety, przez długi czas efekty były mało zadowalające.
Metamateriał powstały z wykorzystaniem technologii druku 3D zapewnia wytrzymałość o 50 procent wyższą niż w przypadku dotychczasowego lidera w tej dziedzinie
Przełom nastąpił dzięki możliwościom oferowanym przez druk 3D. Jak wyjaśniają autorzy, zaczęli od wydrążonej struktury, wewnątrz której rozciągała się cienka taśma. Dzięki takiemu połączeniu członkowie zespołu badawczego uzyskali wytrzymałość i lekkość, jakich nie spotykano do tej pory nawet w świecie natury. Zastosowane podejście pozwoliło na uzyskanie równomiernego rozłożenia naprężeń i ograniczenie występowania słabych punktów w materiale.
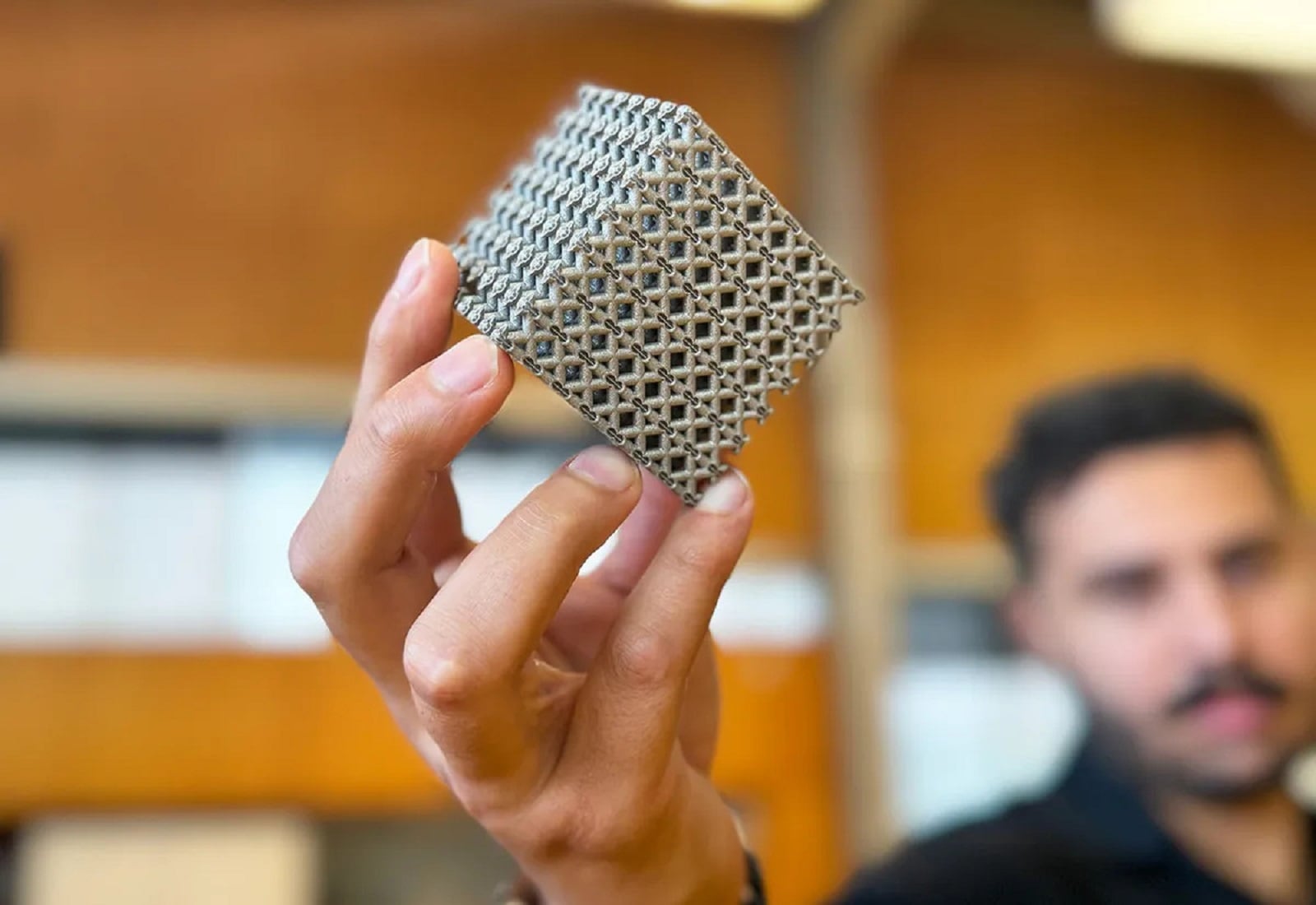
Później trzeba było skorzystać z techniki LPBF (laser powder bed fusion). Wykorzystuje ona wiązkę lasera do stapiania i łączenia warstw proszku metalowego. Efekt końcowy? Tytanowa kostka o 50 procent wytrzymalsza niż odlewany stop magnezu WE54, który nosił do tej pory miano najmocniejszego stopu o podobnej gęstości. Jak wykazały dalsze ekspertyzy, ilość naprężeń występujących w najsłabszych punktach siatki okazała się zredukowana w nowym materiale o połowę.
Czytaj też: Dziwne zjawisko w materiale izolującym metal. Naukowcy przeprowadzili wyjątkowo szczegółowe obserwacje
Bardzo istotny w całej sprawie wydaje się fakt, iż zaprojektowaną strukturę można skalować. Zakres jest ogromny, gdyż mowa o obiektach o wymiarach liczonych od milimetrów do metrów. Naukowcy zwracają również uwagę na biokompatybilność, a także odporność na korozję i ciepło. Wydłuża to listę potencjalnych zastosowań, a autorzy nie zamierzają się zatrzymywać. Choć obecnie ich materiał wytrzymuje temperatury rzędu 350 stopni Celsjusza, to chcieliby zwiększyć próg jego odporności do 600 stopni Celsjusza.