Od stali po aluminium, czyli jak produkować samochody z użyciem drukarek?
Użycie drukarek 3D staje się coraz powszechniejsze nawet w fabrykach. Era używania ich wyłącznie do drukowania prostych elementów z tworzywa sztucznego minęła już dawno. Dziś różnego rodzaju drukarki mogą nie tylko wypluwać z dysz podgrzany filament, ale nawet radzić sobie z wydrukami ze stali czy aluminium. Przypomnieli nam o tym naukowcy z Tohoku University, którzy dorzucili trzy grosze do rozwoju technologii, opracowując swoją własną zaawansowaną technikę druku 3D. Ta umożliwia tworzenie lekkich i trwałych komponentów samochodowych, a jej szczegóły znajdziemy w publikacji obecnej w Additive Manufacturing, które rozwiązują kluczowy problem łączenia różnych materiałów, takich jak stal i aluminium, w projektach wielomateriałowych.
Czytaj też: Naukowcy pokazali swoje nowe dzieło. Czas na rewolucję elektrycznych samochodów
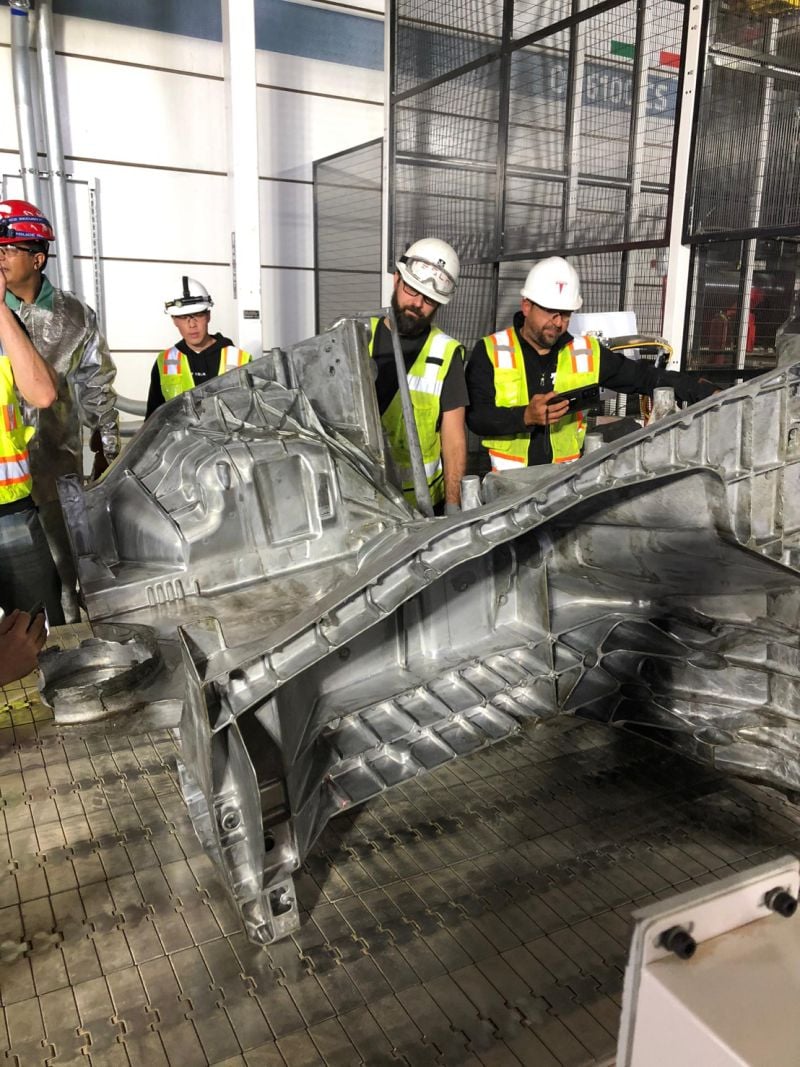
Dla przypomnienia, druk 3D znany również jako wytwarzanie przyrostowe, tworzy obiekty warstwa po warstwie, wykorzystując materiały, takie jak proszki metalowe, które łączą się pod wpływem ciepła. Ta metoda pozwala na produkcję złożonych kształtów przy minimalnym odpadem materiałowym, co stanowi znaczącą przewagę w takich branżach, jak motoryzacja, gdzie waga i wytrzymałość są kluczowe. Wielomateriałowy druk 3D idzie jednak o krok dalej, umożliwiając połączenie różnych materiałów w jednym komponencie, co optymalizuje wydajność. Na przykład połączenie stali z aluminium redukuje wagę przy zachowaniu wysokiej wytrzymałości, ale samo łączenie metali o różnych właściwościach wiąże się z wyzwaniami technicznymi, takimi jak tworzenie się kruchych związków między metalami.
Czytaj też: Ośmieszyli Strefę Czystego Transportu w Warszawie. Stare samochody ciągle w grze
Wspomniany zespół naukowców rozwiązał ten problem, wykorzystując technologię laserowego spiekania proszków metali (L-PBF). Dzięki tej technologii laser precyzyjnie topi proszki metali, pozwalając na dokładną kontrolę nad strukturą drukowanego obiektu. Zwiększając prędkość skanowania lasera, badacze zminimalizowali tworzenie się kruchych związków, tworząc wydruk na granicy stali i aluminium. Wszystko dzięki temu, że przyspieszone skanowanie lasera wywołuje proces zwany niezrównoważoną krystalizacją, który ogranicza rozdzielanie się pierwiastków w stopie. Dzięki temu metale łączą się w sposób trwały i wytrzymały, eliminując typowe problemy związane z wielomateriałowymi komponentami.
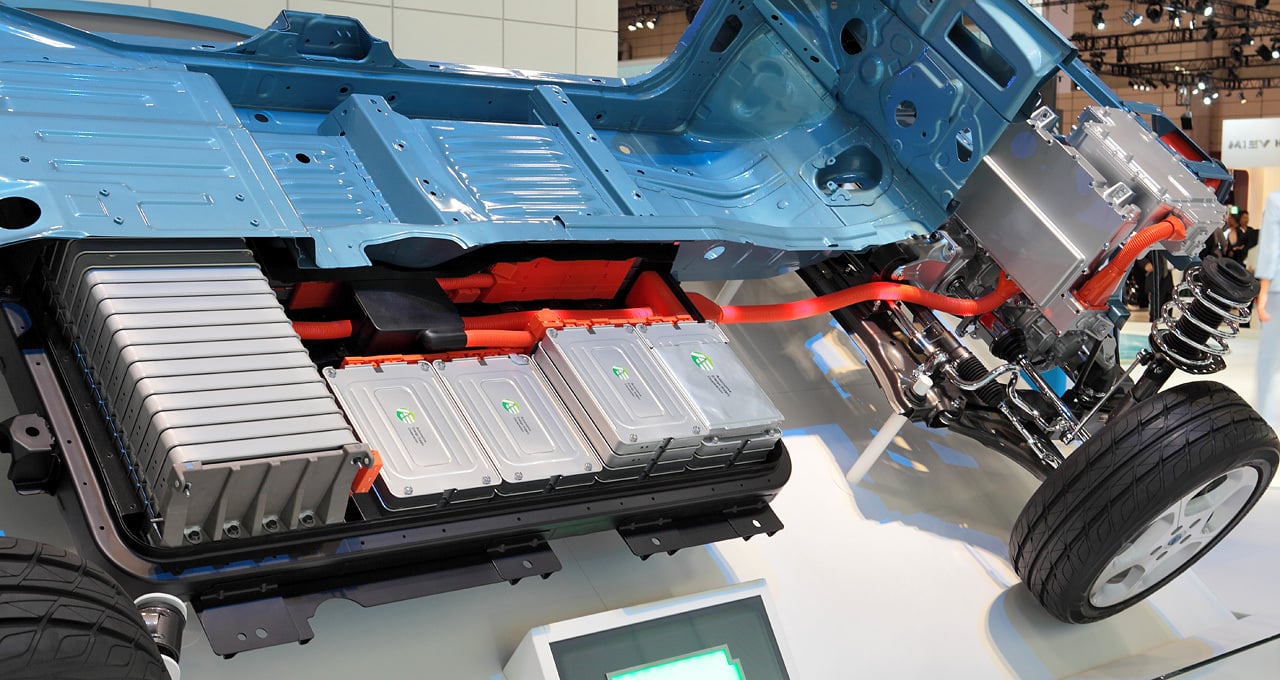
Korzystając z udoskonalonej techniki, naukowcy stworzyli pierwszy na świecie pełnowymiarowy komponent samochodowy wykonany z wielu materiałów – wieżę zawieszenia o zoptymalizowanej geometrii. Prototyp ten pokazuje praktyczne zastosowanie nowej technologii i otwiera drogę do jej wykorzystania w przemyśle motoryzacyjnym i lotniczym. Sukces tego badania otwiera drzwi do dalszych badań nad wielomateriałowym drukiem 3D, bo dalsze udoskonalenie procesów łączenia różnych metali może doprowadzić do produkcji mocniejszych, lżejszych i tańszych komponentów w różnych branżach.
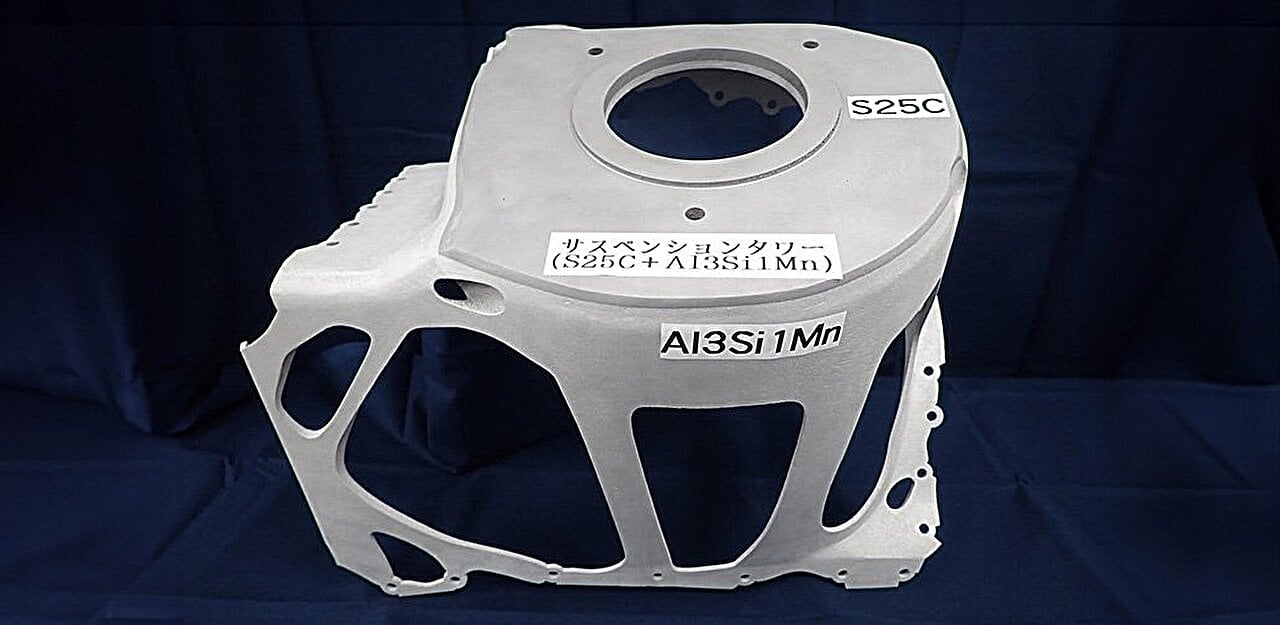
Czytaj też: Sprawdzili akumulatory i oniemieli. Żyłeś w błędzie, a elektryczne samochody są lepsze niż myślisz
Dla producentów samochodów oznacza to ogromne korzyści. Redukcja wagi pojazdów przekłada się bowiem bezpośrednio na lepszą efektywność paliwową i niższe emisje, co z kolei wspiera globalne cele zrównoważonego rozwoju. Ponadto zdolność do produkcji złożonych kształtów z minimalnym odpadem obniża koszty i wspiera ekologiczne praktyki produkcyjne. Pozostaje więc czekać na wdrożenie takiego procesu produkcyjnego do rzeczywistych fabryk.